Opening the Power of Welding WPS: Approaches for Efficiency and Safety And Security in Construction
In the realm of fabrication, Welding Procedure Specs (WPS) stand as the foundation of welding procedures, dictating the essential steps for achieving both efficiency and safety in the construction procedure. Recognizing the intricacies of WPS is paramount to harnessing its complete potential, yet numerous companies have a hard time to open truth power that exists within these files (welding WPS). By diving into the methods that enhance welding WPS, a globe of boosted efficiency and heightened safety waits for those happy to explore the nuances of this important aspect of fabrication

Significance of Welding WPS
The significance of Welding Procedure Specs (WPS) in the fabrication sector can not be overstated. WPS serve as a vital roadmap that lays out the needed actions to make certain welds are carried out constantly and properly. By specifying necessary criteria such as welding procedures, materials, joint designs, preheat temperatures, interpass temperature levels, filler steels, and post-weld heat therapy demands, WPS offer a standardized strategy to welding that improves effectiveness, high quality, and safety and security in manufacture processes.
Adherence to WPS aids in accomplishing uniformity in weld quality, decreasing the probability of problems or structural failings. This standardization likewise promotes conformity with sector policies and codes, making sure that produced frameworks fulfill the needed security criteria. Furthermore, WPS documents allows welders to duplicate effective welding procedures, leading to regular outcomes throughout different tasks.
Fundamentally, the thorough development and rigorous adherence to Welding Treatment Requirements are vital for maintaining the integrity of welded frameworks, guarding against potential threats, and upholding the track record of construction business for supplying top quality products and solutions.
Secret Components of Welding WPS
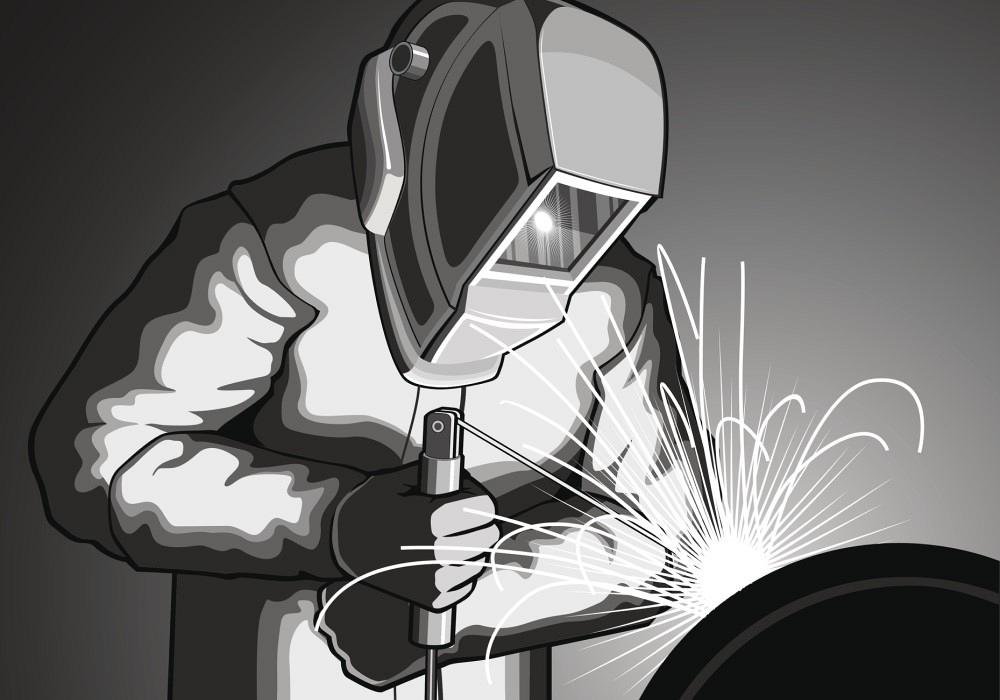
Enhancing Performance With WPS
When enhancing welding operations, leveraging the crucial aspects laid out in Welding Procedure Requirements (WPS) ends up being necessary for maximizing and improving procedures productivity. One means to enhance effectiveness with WPS is by meticulously selecting the appropriate welding specifications. By adhering to the specific guidelines given in the WPS, welders can make certain that the welding tools is established properly, causing top quality and constant welds. Additionally, adhering to the pre-approved welding sequences detailed in the WPS can substantially reduce the moment spent on each weld, inevitably raising total productivity.
Regularly reviewing and upgrading the WPS to integrate any lessons found out or technical developments can also contribute to effectiveness enhancements in welding procedures. By accepting the guidelines set forth in the WPS and continuously seeking means to optimize processes, fabricators can accomplish greater effectiveness levels and superior end outcomes.
Ensuring Safety And Security in Construction

Safety and security procedures in manufacture play a pivotal duty in securing personnel and maximizing operational treatments. Making certain safety in construction includes a diverse approach that includes different facets of the welding process. One basic element is the stipulation of individual safety tools (PPE) tailored to the specific threats existing in the fabrication atmosphere. Welders need to be outfitted with proper equipment such as headgears, handwear covers, and protective clothes to reduce risks connected with welding activities.
Moreover, adherence to proper ventilation and fume removal systems is important in keeping a healthy and website link balanced job atmosphere. Welding fumes include dangerous compounds that, if breathed in, can position major health dangers. Applying reliable air flow actions helps to reduce exposure to these dangerous fumes, promoting respiratory health and wellness amongst workers.
Routine devices upkeep and examinations are likewise vital for ensuring safety and security in manufacture. Damaged machinery can cause crashes and injuries, highlighting the importance of prompt repairs and regular checks. By focusing on precaution and cultivating a culture of understanding, fabrication centers can produce a efficient and protected workplace for their workers.
Applying WPS Finest Practices
To improve operational efficiency and guarantee high quality end results in fabrication procedures, reference incorporating Welding Procedure Spec (WPS) best practices is extremely important - welding WPS. Carrying out WPS ideal practices entails meticulous planning, adherence to industry requirements, and constant surveillance to ensure ideal outcomes. First of all, picking the appropriate welding procedure, filler material, and preheat temperature level defined in the WPS is critical for attaining the desired weld high quality. Second of all, guaranteeing that certified welders with the necessary certifications carry out the welding procedures according to the WPS standards is essential for consistency and dependability. Consistently reviewing and upgrading WPS documents to reflect any kind of procedure renovations or adjustments in materials is additionally a vital finest practice to keep precision and importance. In addition, giving detailed training to welding employees on WPS needs and finest description practices cultivates a culture of safety and security and top quality within the construction setting. By faithfully applying WPS finest techniques, producers can streamline their procedures, reduce mistakes, and provide remarkable products to satisfy client assumptions.
Conclusion
In verdict, welding WPS plays a critical function in making sure performance and safety in fabrication procedures. By complying with these methods, services can unlock the complete capacity of welding WPS in their manufacture operations.
In the world of construction, Welding Treatment Requirements (WPS) stand as the backbone of welding operations, determining the needed steps for achieving both effectiveness and safety in the manufacture process. By specifying essential parameters such as welding procedures, products, joint styles, preheat temperatures, interpass temperature levels, filler metals, and post-weld warm treatment requirements, WPS offer a standard approach to welding that improves performance, quality, and security in manufacture processes.
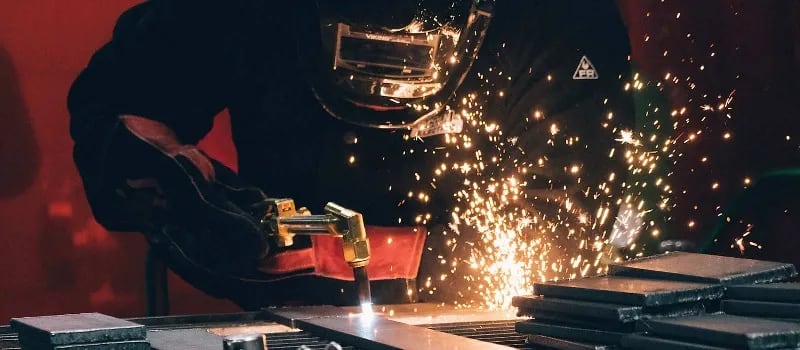
When optimizing welding procedures, leveraging the key aspects described in Welding Procedure Specifications (WPS) becomes important for maximizing and improving procedures efficiency. (welding WPS)